The KODAK FLEXCEL NX System was developed to solve fundamental challenges in flexo printing. PureFlexoâ„¢ Printing builds on over a decade of flexo innovation and expertise in highly controlled ink transfer mechanisms to address the sources of unwanted ink spread for the first time, helping flexible packaging printers bring optimized efficiency to the press room.
With the introduction of PureFlexo Printing this month, it’s the ideal time to reflect on Miraclon’s rich heritage of innovation since the first FLEXCEL NX System was introduced in 2008.
The FLEXCEL NX System, launched in 2008, brought a new level of consistency and quality to flexo through pixel-for-pixel image reproduction. Prepress could move on from guesswork and printers could rely on predictable press performance.
The imaging approach and pioneering use of flat top dots created new highs in resolution, consistently recreating brand designs and top graphic quality on flexible packing.
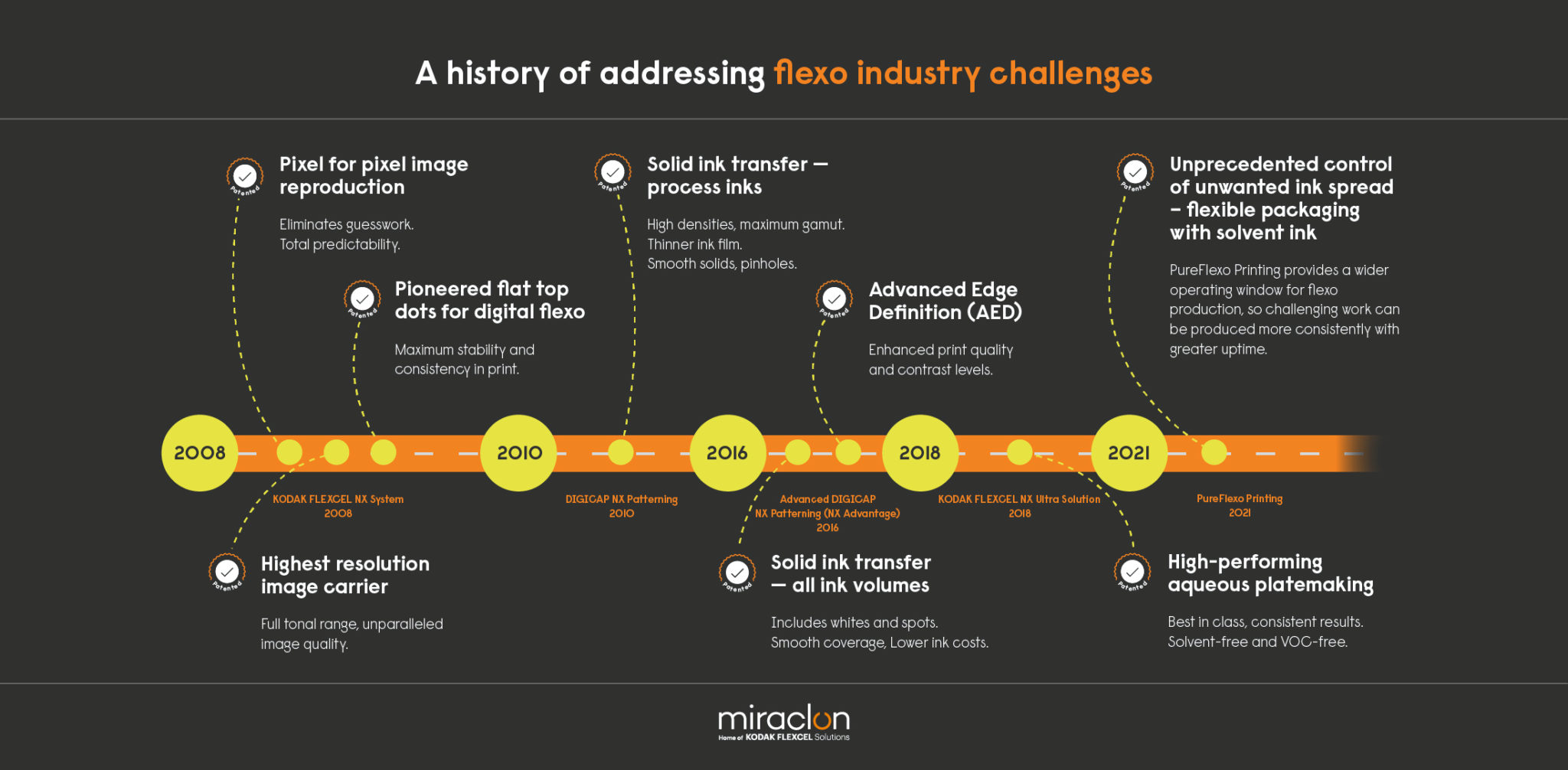
Back to the roots
In the years that followed, FLEXCEL NX System research and innovation has focused on solving the fundamental challenges of flexo printing by establishing the reasons why challenges occur and finding solutions, rather than searching for fixes that would mask problems in production.
Developments included steps forward in ink transfer, first with the introduction of DIGICAP NX Patterning in 2010, followed by Advanced DIGICAP NX Patterning (commonly referred to as NX Advantage) with Advanced Edge Definition technology in 2016. These improvements in ink transfer helped to cement flexo’s position as a leading printing method for any brand, winning work from other processes, once prized for their superior quality.
The past two years have seen some of that R&D focus turn to unwanted ink spread, a fundamental flexo feature and one that can put pressure on productivity and profits throughout the flexible packaging value chain.
With flexo printing moving to higher line screens, better graphics and photorealistic imagery, that eye-catching print performance was reproduced in aqueous platemaking with the introduction of our FLEXCEL NX ULTRA Solution in 2018.
Time to reset the quality-efficiency balance
The R&D team delivering innovations to the industry today is much the same as the team who brought the FLEXCEL NX System to life following its introduction, building on that patented technology.
The past two years have seen some of our R&D focus turn to unwanted ink spread, a fundamental issue in flexo printing – especially with solvent ink on wide web flexible packaging applications – and one that can put pressure on productivity and profits throughout the flexible packaging value chain.
Instead of tackling the symptoms, we’ve gone to the root of the problem, using our knowledge of ink transfer and plate surface technology
On the production floor, the symptoms of ink spread – dot bridging, visible color voids, ink starvation, trailing edge voids – are being tackled through high impression, harder anilox tapes and ink viscosity adjustment. Trying to reduce the effects of unwanted ink spread often creates other issues on the press and doesn’t solve the problem.
Instead of tackling the symptoms, we’ve gone to the root of the problem, using our knowledge of ink transfer and plate surface technology to give printers more ink control for a streamlined, robust flexible packaging printing process and more predictable prepress.
Building on the core competencies of the FLEXCEL NX System, PureFlexo Printing addresses the causes of unwanted ink spread in wide web solvent ink on film applications for the first time, putting new confidence into color management and giving printers more control on press.
It delivers new levels of control over ink spread, for a wider print latitude, resetting the quality-efficiency balance.
DISCOVER CLEANER, MORE EFFICIENT FLEXO. PURE FLEXO PRINTING with KODAK FLEXCEL NXÂ